Aluminum composite panel cutting is a crucial process in the manufacturing of various products. These panels are widely used in the construction industry due to their lightweight, durability, and versatility. They are commonly used for cladding, roofing, and signage, among other applications. However, cutting them requires specialized tools and techniques to ensure accuracy and efficiency.
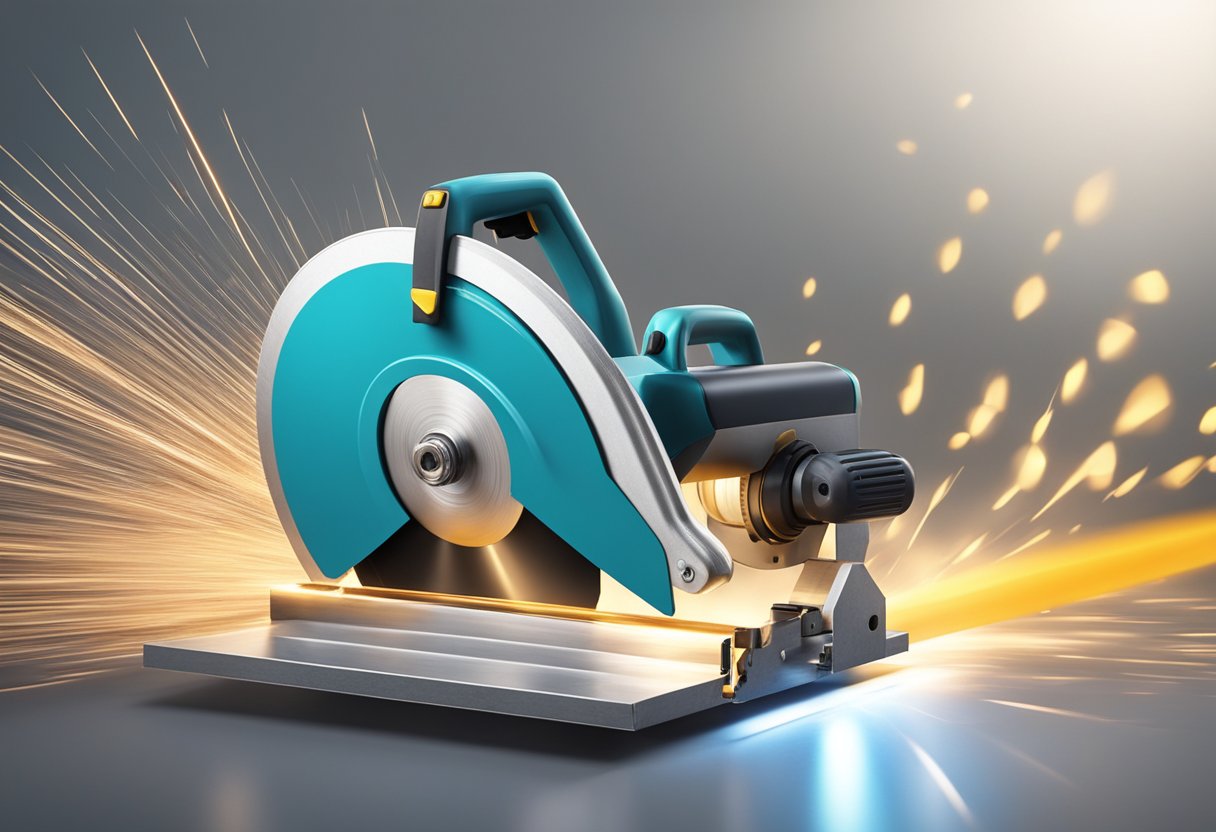
One of the most popular methods of cutting aluminum composite panels is using a CNC router. This computer-controlled machine can precisely cut the panels to the required size and shape, ensuring a high-quality finish. Another method is using a panel saw, which is a manual or semi-automatic machine that can cut multiple panels at once. Both methods require a skilled operator who can program the machine and ensure the accuracy of the cuts.
Basics of Aluminum Composite Panel Cutting
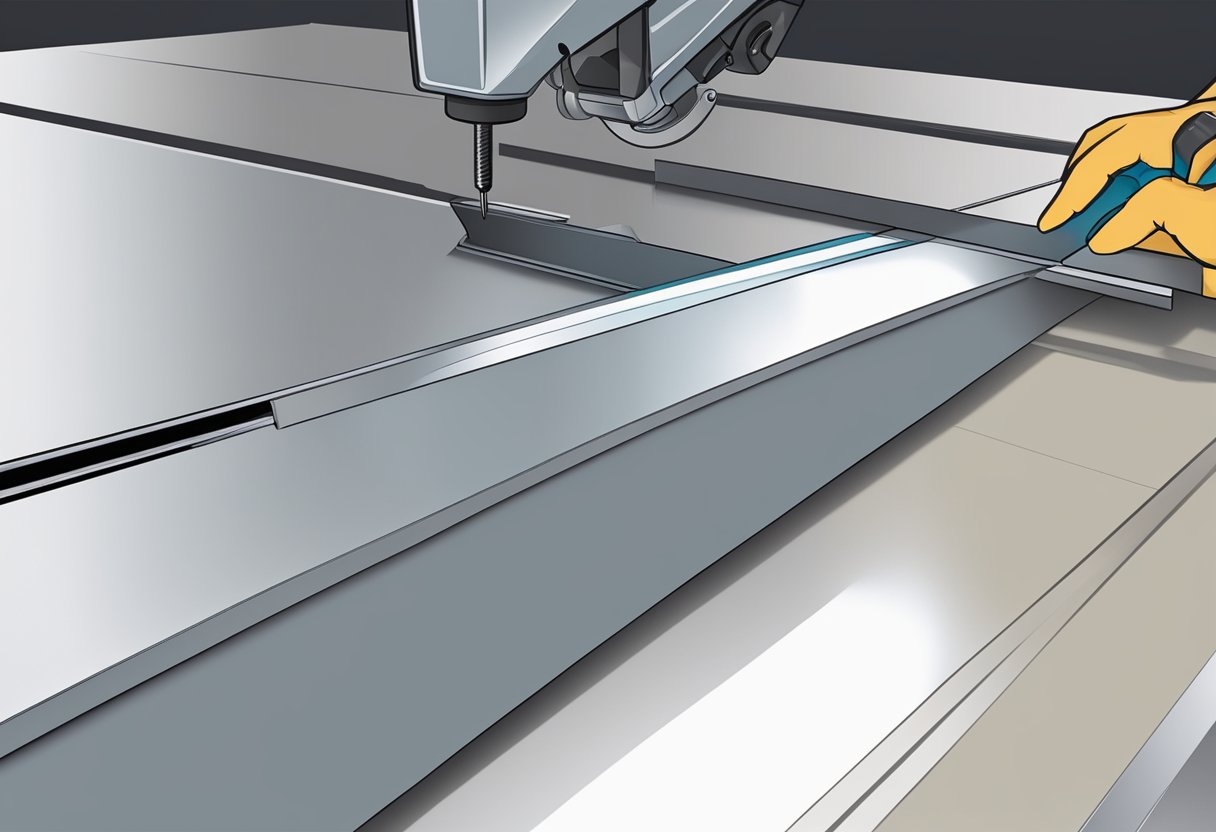
Aluminum Composite Panels (ACPs) are widely used in the construction industry due to their durability, lightweight, and aesthetic appeal. Cutting these panels can be challenging, but with the right tools and techniques, it can be done quickly and accurately.
Tools for Cutting ACPs
To cut ACPs, one needs a circular saw or a router with a carbide-tipped blade. A circular saw is preferred for straight cuts, while a router is used for curves and intricate shapes. The blade or bit should have a high tooth count to ensure a smooth finish.
Techniques for Cutting ACPs
Before cutting, one should measure and mark the panel carefully. A straight edge or a T-square can be used to ensure accurate measurements. ACPs should be cut with the protective film facing down to prevent scratching.
When cutting with a circular saw, one should use a guide to ensure a straight cut. The blade should be set to the appropriate depth to prevent damage to the core material. The panel should be clamped securely to prevent movement during cutting.
When cutting with a router, one should use a template to guide the bit. The bit should be set to the appropriate depth to prevent damage to the core material. The panel should be clamped securely to prevent movement during cutting.
Safety Precautions
When cutting ACPs, one should wear appropriate personal protective equipment, including safety glasses, gloves, and a dust mask. The saw or router should be operated according to the manufacturer’s instructions.
Cutting ACPs requires the right tools and techniques to ensure a smooth and accurate finish. With proper safety precautions, one can achieve a professional result when cutting ACPs.
Safety Precautions for Cutting Aluminum Composite Panels
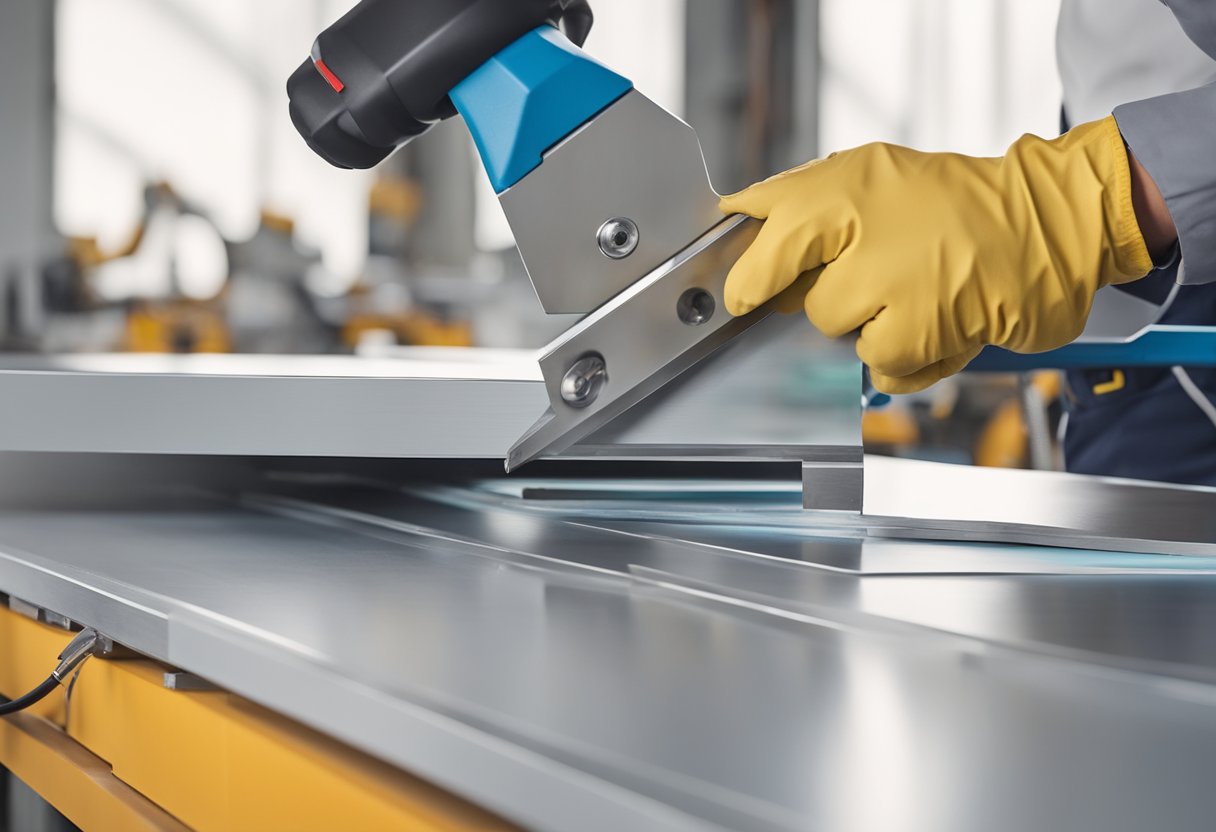
Personal Protective Equipment
When cutting aluminum composite panels, it is essential to wear appropriate personal protective equipment (PPE) to prevent injuries. PPE includes safety glasses, earplugs, gloves, and a dust mask. Safety glasses protect the eyes from flying debris, while earplugs protect the ears from loud noises produced by the cutting tools. Gloves protect the hands from cuts and abrasions, and a dust mask protects the lungs from inhaling harmful particles.
Workspace Setup and Safety
The workspace should be set up in a way that ensures safety. The workspace should be well-ventilated to prevent the accumulation of harmful dust particles. The cutting tools should be placed on a stable surface to prevent them from falling. The workspace should be free of clutter to avoid tripping hazards.
It is important to use the correct cutting tool for the job. The cutting tool should be sharp and in good condition. Dull cutting tools can cause accidents and produce poor-quality cuts. The cutting tool should be securely fastened to the cutting machine to prevent it from coming loose during operation.
Safety should always be a top priority when cutting aluminum panels. By following the safety precautions outlined above, workers can minimize the risk of injury and ensure a safe working environment.
Tools for Cutting Aluminum Composite Panels
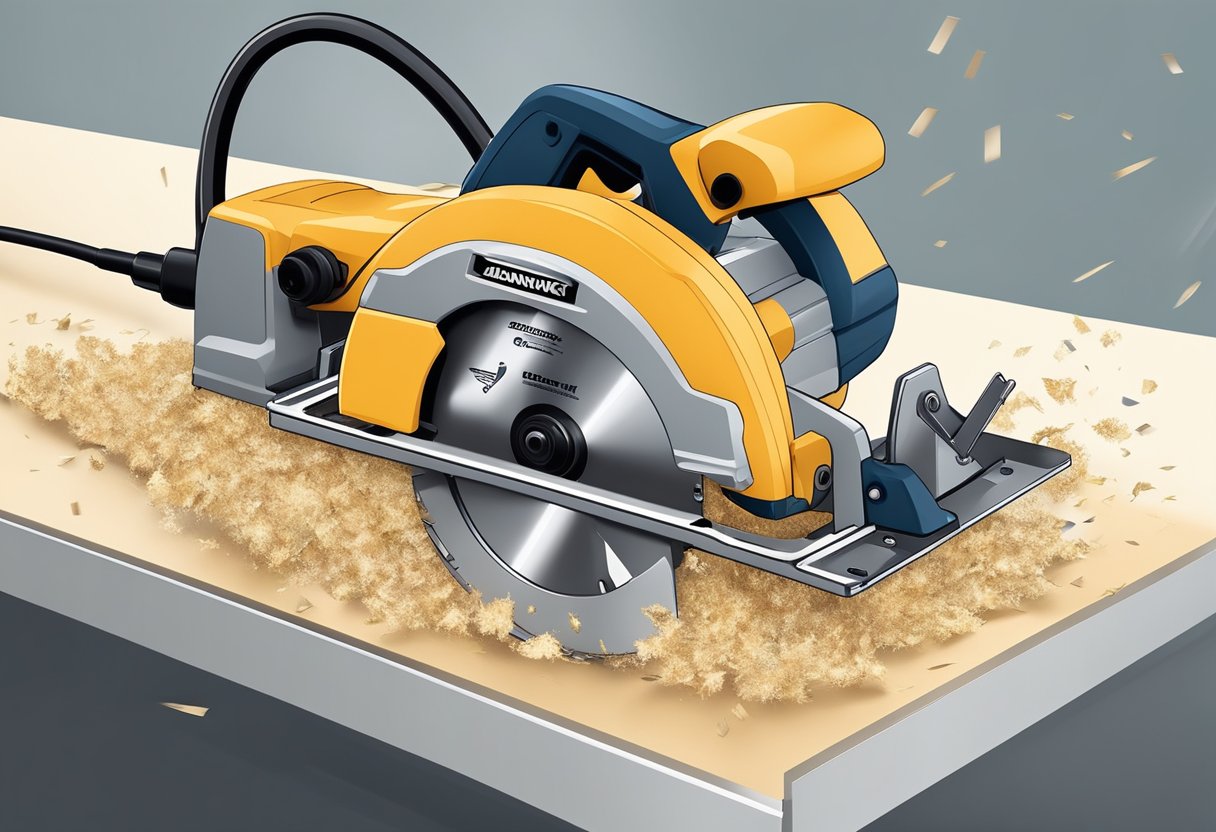
Aluminum composite panels (ACP) are widely used in construction and architecture because of their durability, light weight, and aesthetic appeal. However, cutting ACP can be challenging, and it requires the right tools and techniques. In this section, we will discuss the most common tools used for cutting ACP.
Manual Cutting Tools
Manual cutting tools are suitable for small-scale cutting tasks and are ideal for cutting curves and shapes. The following are some of the most commonly used manual cutting tools for ACP:
- Utility Knife: A utility knife is a versatile cutting tool that can be used to cut ACP sheets. It is best for making small cuts and trimming the edges of the panels.
- Jigsaw: A jigsaw is a handheld saw that can be used to cut curves and intricate shapes in ACP sheets. It is a versatile tool that can be used to cut through different materials.
- Handsaw: A handsaw is a manual cutting tool that can be used to cut ACP sheets. It is best for making straight cuts and is suitable for cutting thicker panels.
Power Cutting Tools
Power cutting tools are ideal for cutting large volumes of ACP sheets quickly and accurately. The following are some of the most commonly used power cutting tools for ACP:
- Circular Saw: A circular saw is a powerful cutting tool that can be used to cut ACP sheets. It is best for making straight cuts and is suitable for cutting thicker panels.
- Router: A router is a power tool that can be used to cut intricate shapes and designs in ACP sheets. It is ideal for cutting decorative panels and can be used to create grooves and channels in the panels.
- Guillotine Shear: A guillotine shear is a power tool that can be used to cut ACP sheets quickly and accurately. It is ideal for cutting large volumes of panels and is suitable for cutting thicker panels.
In conclusion, choosing the right cutting tool for ACP is essential for achieving accurate and clean cuts. Manual cutting tools are suitable for small-scale cutting tasks, while power cutting tools are ideal for cutting large volumes of panels quickly and accurately.
Measuring and Marking for Precision Cutting
Measuring Techniques
Before cutting aluminum composite panels (ACP), it is important to measure and mark the panels accurately to ensure precise cuts. There are several measuring techniques that can be used to achieve this goal.
One technique is to use a tape measure to measure the length and width of the panel. It is important to make sure the tape measure is straight and level to get accurate measurements. Another technique is to use a square to mark straight lines for cutting. A combination square can be used to mark angles as well.
Marking Tools
Once the measurements have been taken, the next step is to mark the panel for cutting. There are several marking tools that can be used for this purpose.
A pencil is a common marking tool that can be used to mark straight lines. However, it is important to use a sharp pencil and make sure the line is dark enough to be visible. Another option is to use a marker, which can create a more visible line.
In addition to pencils and markers, there are specialized marking tools that can be used for more precise marking. For example, a scribe can be used to make a fine line that is easy to follow when cutting. A center punch can be used to make a small indentation that can guide the drill bit when making holes.
By using precise measuring and marking techniques, you can ensure that your cuts are accurate and your aluminum composite panels fit perfectly.
Cutting Techniques for Aluminum Composite Panels
Straight Cuts
When cutting aluminum composite panels, it is important to use the right tools and techniques to ensure a clean and accurate cut. One of the most common cutting techniques for aluminum composite panels is a straight cut. This can be achieved using a circular saw or a panel saw with a fine-toothed blade.
Before making the cut, it is important to mark the panel accurately to ensure a straight cut. A straight edge or a T-square can be used to mark the panel. Once the panel is marked, it can be clamped securely to a workbench or sawhorse to prevent it from moving during the cut.
When using a circular saw, it is important to use a fine-toothed blade with a high tooth count to ensure a clean cut. The blade should also be sharp to prevent it from tearing or chipping the panel. When making the cut, it is important to move the saw at a slow and steady pace to prevent the blade from overheating and to ensure a smooth cut.
Curved Cuts
Aluminum composite panels can also be cut into curved shapes using a jigsaw or a router. This can be useful for creating custom shapes and designs.
Before making the cut, it is important to mark the panel accurately to ensure a smooth and accurate curve. A compass or a template can be used to mark the panel. Once the panel is marked, it can be clamped securely to a workbench or sawhorse to prevent it from moving during the cut.
When using a jigsaw or a router, it is important to use a fine-toothed blade or a router bit with a high tooth count to ensure a clean cut. The blade or bit should also be sharp to prevent it from tearing or chipping the panel. When making the cut, it is important to move the tool at a slow and steady pace to prevent it from overheating and to ensure a smooth cut.
Overall, cutting aluminum composite panels requires the right tools and techniques to ensure a clean and accurate cut. By following these techniques, it is possible to achieve a professional-looking finish for any project.
CNC Machining of Aluminum Composite Panels
Programming CNC Machines
CNC machining is a popular method for cutting aluminum composite panels due to its precision and efficiency. To program a CNC machine for cutting aluminum composite panels, the operator must input the design specifications into the machine’s software. This includes the dimensions of the panel, the desired shape and pattern, and the cutting tool to be used.
The software then generates a toolpath, which is a set of instructions for the machine to follow. The toolpath determines the movement of the cutting tool, including the direction, speed, and depth of the cut. It is important to ensure that the toolpath is accurate and efficient to minimize waste and maximize productivity.
Operation and Maintenance
Once the CNC machine is programmed, it is ready for operation. The operator must ensure that the machine is properly set up and calibrated before beginning the cutting process. This includes checking the alignment of the cutting tool and the panel, as well as ensuring that the machine is running at the correct speed and feed rate.
During operation, it is important to monitor the cutting process to ensure that the machine is cutting accurately and efficiently. This includes checking for any signs of wear or damage to the cutting tool, as well as monitoring the quality of the cut.
Regular maintenance is also essential to ensure that the CNC machine is operating at peak performance. This includes cleaning and lubricating the machine, as well as replacing any worn or damaged parts. By following proper maintenance procedures, the operator can extend the life of the machine and ensure consistent, high-quality cuts.
In conclusion, CNC machining is an effective method for cutting aluminum composite panels. By properly programming and operating the machine, and following regular maintenance procedures, operators can achieve precise, efficient cuts that meet the design specifications.
Finishing Edges After Cutting
Cutting aluminum composite panels can leave sharp or rough edges that need to be finished to ensure safety and a professional appearance. There are several methods for finishing edges after cutting, including deburring and edge profiling.
Deburring Methods
Deburring is the process of removing burrs or rough edges from the cut edge of the panel. There are several methods for deburring aluminum composite panels, including:
- Hand filing: This method involves using a file to manually remove burrs and rough edges. It is a cost-effective method but can be time-consuming and less precise than other methods.
- Sanding: Sandpaper or sanding discs can be used to remove burrs and rough edges. This method is faster than hand filing and can produce a smoother finish but may require more skill to achieve a consistent edge.
- Deburring tools: There are specialized deburring tools available that can quickly and easily remove burrs and rough edges. These tools can be expensive but are precise and efficient.
Edge Profiling
Edge profiling is the process of shaping or beveling the cut edge of the panel for a more finished appearance. There are several methods for edge profiling aluminum composite panels, including:
- Router: A router can be used to create a beveled edge or decorative profile on the cut edge of the panel. This method requires skill and experience to achieve a consistent and precise finish.
- Edge trim: Edge trim can be applied to the cut edge of the panel to cover any rough or unfinished edges. This method is quick and easy but may not provide as polished of a finish as other methods.
- CNC cutting: Computer numerical control (CNC) cutting machines can be programmed to create precise and consistent edge profiles on aluminum composite panels. This method is efficient and accurate but requires specialized equipment and expertise.
In conclusion, finishing the edges of aluminum composite panels after cutting is an important step in ensuring safety and a professional appearance. There are several methods for deburring and edge profiling, each with their own advantages and disadvantages. By selecting the appropriate method for their project, users can achieve a finished product that meets their needs and requirements.
Joining Cut Aluminum Composite Panels
When it comes to joining cut aluminum composite panels, there are two primary methods: adhesive bonding and mechanical fastening.
Adhesive Bonding
Adhesive bonding is a popular method for joining cut aluminum composite panels. This method involves using an adhesive to bond the panels together. The adhesive is applied to the surface of the panel and then the two panels are pressed together until the adhesive dries.
One advantage of adhesive bonding is that it creates a seamless join between the two panels. This method also provides a strong bond that is resistant to weathering and other environmental factors. However, it is important to note that not all adhesives are suitable for use with aluminum composite panels. It is important to choose an adhesive that is specifically designed for this purpose.
Mechanical Fastening
Mechanical fastening involves using screws, bolts, or other mechanical fasteners to join the panels together. This method is often used in conjunction with adhesive bonding to provide additional strength and stability.
One advantage of mechanical fastening is that it allows for easy disassembly if needed. This method is also ideal for applications where the panels will be subjected to significant stress or movement.
It is important to note that the choice of joining method will depend on the specific application and the requirements of the project. Both adhesive bonding and mechanical fastening can provide a strong and reliable join between cut aluminum composite panels.
Troubleshooting Common Cutting Issues
Material Chipping
One of the most common cutting issues faced while working with aluminum composite panels is material chipping. This can occur due to various reasons such as dull blades, incorrect cutting speeds, or improper blade alignment.
To prevent material chipping, it is recommended to use sharp blades and ensure that the cutting speed is appropriate for the thickness of the panel. Additionally, the blade should be aligned properly to ensure a smooth cut.
Inaccurate Cuts
Another common issue while cutting aluminum composite panels is inaccurate cuts. This can be caused by a variety of factors such as incorrect blade depth, improper blade angle, or incorrect feed rate.
To avoid inaccurate cuts, it is important to ensure that the blade depth and angle are set correctly. Additionally, the feed rate should be adjusted to match the thickness of the panel being cut.
By following these troubleshooting tips, users can achieve clean and accurate cuts while working with aluminum composite panels.
Waste Management and Recycling Cut-Offs
Recycling Practices
Aluminum composite panels have a high recycling value due to the aluminum content. The recycling process involves separating the aluminum from the plastic core, which can then be reused. Recycling aluminum saves energy and reduces the amount of waste sent to landfills.
Manufacturers and suppliers of aluminum composite panels often have recycling programs in place to collect waste materials and recycle them. These programs can help reduce the environmental impact of the manufacturing process and provide a sustainable solution for waste management.
Waste Reduction Techniques
To minimize waste during the cutting process, it is important to plan the layout of the panels carefully. This can help reduce the amount of material that is wasted due to improper cuts or unused sections.
Another technique to reduce waste is to use a computer-aided cutting system. These systems can optimize the layout of the panels to reduce waste and increase efficiency.
Additionally, it is important to properly dispose of any waste material that is generated during the cutting process. This can include scraps of aluminum and plastic. Recycling programs can help ensure that waste materials are disposed of in an environmentally friendly manner.
Overall, implementing recycling practices and waste reduction techniques can help reduce the environmental impact of aluminum composite panel cutting. By properly managing waste materials, manufacturers and suppliers can promote sustainability and reduce their carbon footprint.