Aluminum panel extrusions have become an increasingly popular choice for architects and designers due to their versatility, durability, and aesthetic appeal. These extrusions are made by shaping aluminum into a specific profile, which can then be used to create a variety of finished products, including building facades, curtain walls, and decorative elements.
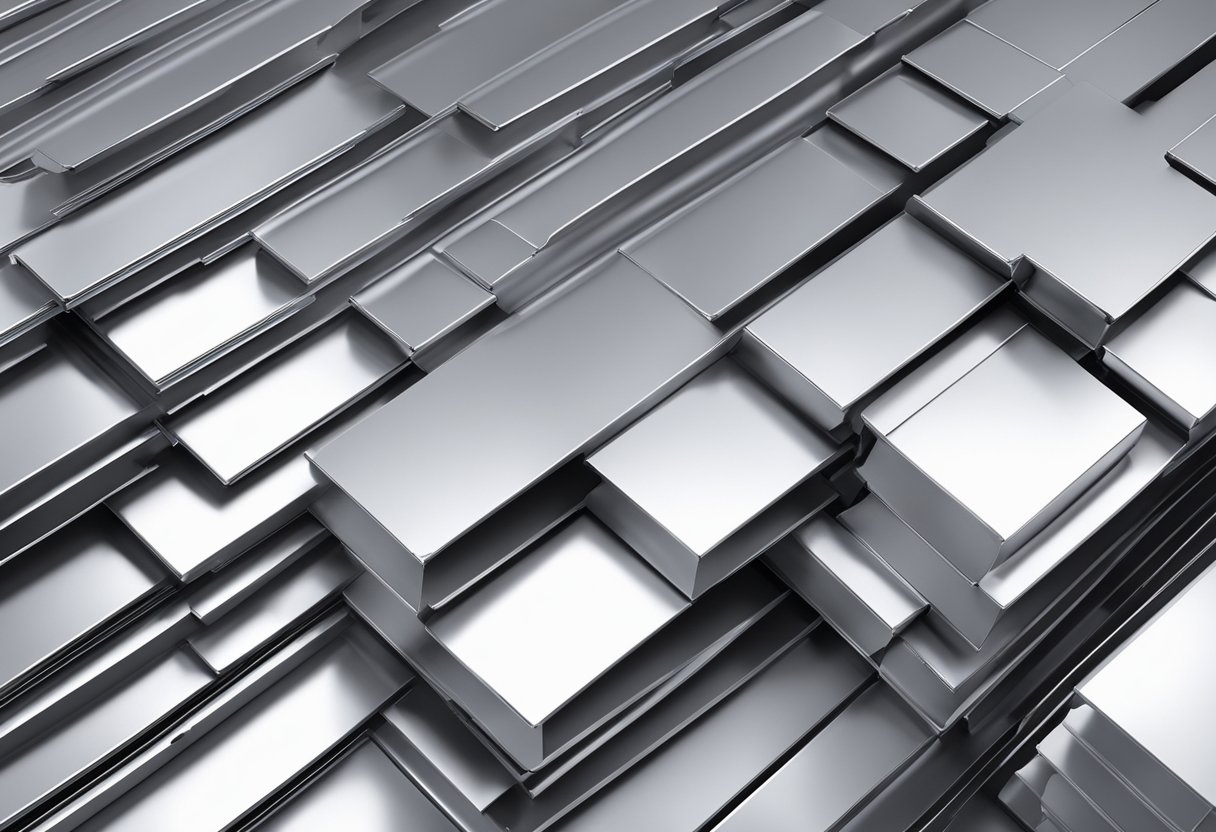
One of the key benefits of aluminum panel extrusions is their lightweight nature, which makes them easy to transport and install. Additionally, aluminum is a highly durable material that is resistant to corrosion, making it an ideal choice for use in outdoor environments. These extrusions can also be finished in a variety of colors and textures, providing architects and designers with a wide range of options to choose from when creating their designs.
Overall, aluminum panel extrusions offer a range of benefits that make them an attractive choice for architects and designers. With their versatility, durability, and aesthetic appeal, they are sure to continue to be a popular choice in the construction industry for years to come.
Basics of Aluminum Panel Extrusions
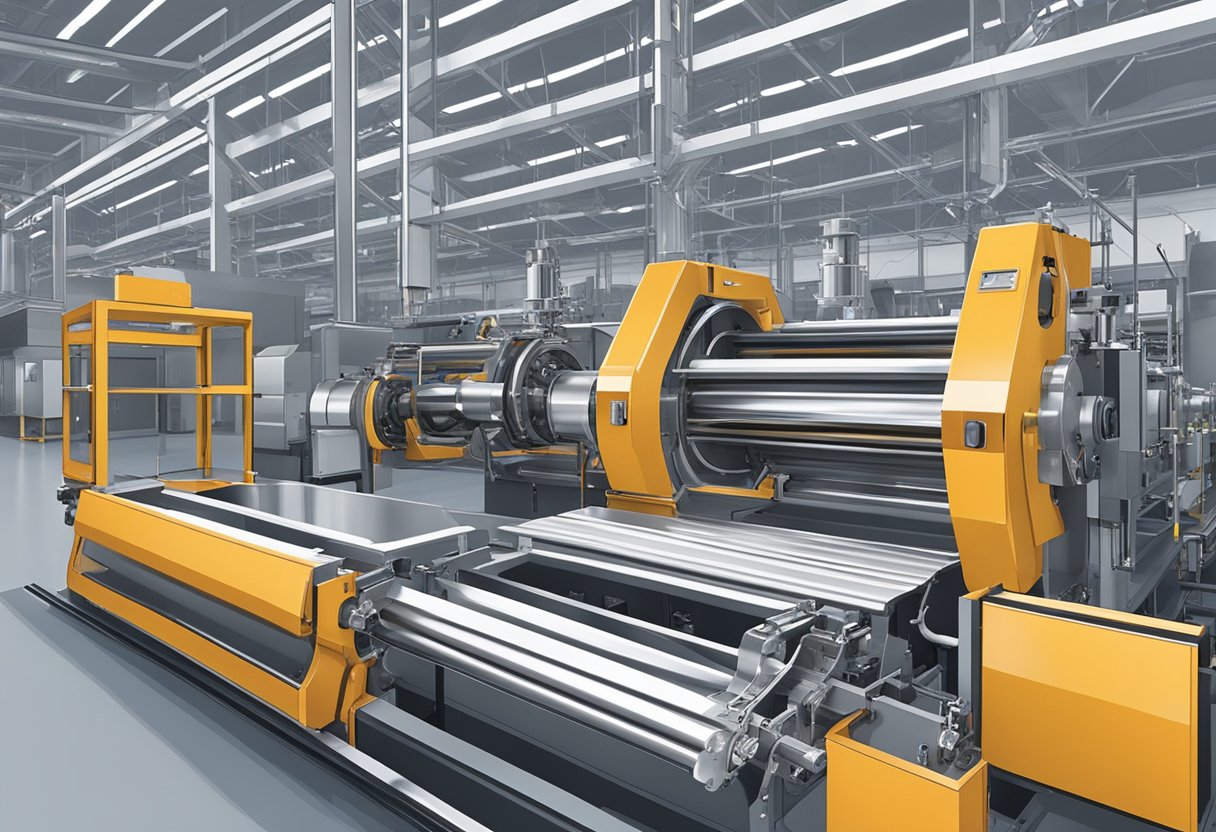
Aluminum panel extrusions are a popular choice for building facades and cladding due to their durability, lightweight, and aesthetic appeal. The extrusion process involves shaping aluminum alloy into a specific profile using a die and an extrusion press. The resulting panel can be cut to length and assembled into a variety of configurations to suit the design requirements of the building.
Aluminum panel extrusions offer a range of benefits over other materials such as steel, wood, and concrete. They are corrosion-resistant, fire-resistant, and require minimal maintenance. Additionally, aluminum is highly recyclable, making it an environmentally-friendly choice for building materials.
The extrusion process allows for a high degree of customization, with a variety of finishes and colors available to suit the design intent. The panels can also be perforated or embossed to add texture and visual interest.
Overall, aluminum panel extrusions are a versatile and reliable choice for building facades and cladding. Their durability, lightweight, and aesthetic appeal make them a popular choice for architects and builders alike.
Manufacturing Processes
Extrusion Technique
Aluminum panel extrusions are manufactured using an extrusion process. This process involves heating a cylindrical aluminum billet until it is soft enough to be pushed through a die to create a desired shape. The extrusion process allows for a variety of shapes and sizes to be produced with a high degree of precision. The extruded aluminum panels are typically used in construction and architecture due to their lightweight and durability.
The extrusion process begins with the creation of a die, which is a custom-made tool that determines the shape and size of the extruded aluminum panel. The die is made from hardened steel and is designed to withstand the high pressures and temperatures required for the extrusion process.
Once the die is created, the aluminum billet is heated to a specific temperature and then pushed through the die using a hydraulic press. The extruded aluminum panel is then cooled and cut to the desired length.
Cutting and Finishing
After the extrusion process is complete, the aluminum panel must be cut and finished to the desired specifications. Cutting is typically done using a saw or other cutting tool, and finishing can include processes such as sanding, polishing, or painting.
One common finishing technique for aluminum panels is anodizing. Anodizing is an electrochemical process that creates a protective layer on the surface of the aluminum, which helps to prevent corrosion and increase durability. Anodized aluminum panels are commonly used in outdoor applications due to their ability to withstand harsh weather conditions.
Overall, the manufacturing processes involved in creating aluminum panel extrusions require a high degree of precision and expertise. However, the resulting products are lightweight, durable, and highly versatile, making them a popular choice for a variety of construction and architectural applications.
Properties and Specifications
Material Properties
Aluminum panel extrusions are known for their excellent strength-to-weight ratio, making them a popular choice for various construction projects. These panels are made from high-quality aluminum alloys that offer exceptional durability and corrosion resistance. Additionally, aluminum is a highly malleable material that can be easily shaped and formed into complex designs.
The thickness of the aluminum panel extrusions can vary depending on the specific application and load requirements. The panels can range from 1mm to 8mm in thickness, with the most common thickness being 3mm. The surface finish of the panels can also be customized to meet the specific needs of the project.
Standard Dimensions
Aluminum panel extrusions come in a variety of standard dimensions to meet the needs of different applications. The standard dimensions for these panels include:
- Width: 1220mm, 1500mm, and 2000mm
- Length: 2440mm, 3000mm, and 6000mm
- Thickness: 3mm, 4mm, and 6mm
These standard dimensions can be customized to meet the specific requirements of the project. The panels can also be cut to size and shape to fit the design needs of the project.
Overall, aluminum panel extrusions offer a range of properties and specifications that make them a versatile and reliable choice for various construction projects.
Applications of Aluminum Panel Extrusions
Aluminum panel extrusions have a wide range of applications in both architectural and industrial fields. These extrusions are lightweight, durable, and corrosion-resistant, making them a popular choice for many applications.
Architectural Uses
Aluminum panel extrusions are commonly used in architectural applications such as building facades, curtain walls, and roofing systems. These extrusions offer a sleek and modern look to buildings, while also providing excellent thermal and acoustic insulation.
In addition to their aesthetic appeal, aluminum panel extrusions are also highly customizable. They can be fabricated in a variety of shapes and sizes to meet the specific needs of a project. This makes them an ideal choice for architects and designers who want to create unique and innovative building designs.
Industrial Applications
Aluminum panel extrusions are also widely used in various industrial applications. They are commonly used in the transportation industry for the construction of trailers, truck bodies, and railcars. These extrusions offer excellent strength-to-weight ratio, making them an ideal choice for applications where weight is a critical factor.
In addition to their use in transportation, aluminum panel extrusions are also used in the manufacturing of industrial equipment and machinery. They offer excellent corrosion resistance, making them suitable for use in harsh environments.
Overall, aluminum panel extrusions offer a versatile and cost-effective solution for a wide range of applications in both architectural and industrial fields. With their excellent properties, they are sure to remain a popular choice for many years to come.
Installation and Maintenance
Installation Guidelines
When it comes to installing aluminum panel extrusions, it is important to follow the manufacturer’s guidelines carefully. The first step is to make sure that the surface where the panels will be installed is clean and free of any debris or contaminants. Any protrusions or rough spots on the surface should be smoothed out to ensure a flat and even installation.
Next, the panels should be cut to the appropriate size and shape, taking into account any necessary allowances for expansion and contraction. The panels should be installed using the appropriate fasteners and sealants, as recommended by the manufacturer. It is important to ensure that the panels are securely fastened, but not over-tightened, which could cause damage to the panels or the underlying structure.
During installation, it is also important to take into account any potential environmental factors, such as wind and weather conditions. Panels should be installed in a way that minimizes the risk of damage from these factors, and any necessary precautions should be taken to ensure that the panels remain securely in place.
Maintenance Tips
Proper maintenance is key to ensuring the longevity and performance of aluminum panel extrusions. Regular cleaning is important to remove any dirt or debris that may accumulate on the surface of the panels, which could potentially cause damage or discoloration over time.
It is also important to regularly inspect the panels for any signs of damage or wear, such as cracks, dents, or scratches. Any damage should be repaired promptly to prevent further damage or deterioration.
In addition, it is important to ensure that any sealants or coatings used on the panels are in good condition, and to reapply them as necessary to maintain their effectiveness.
By following these installation and maintenance guidelines, users can ensure that their aluminum panel extrusions remain in good condition and provide reliable performance over the long term.