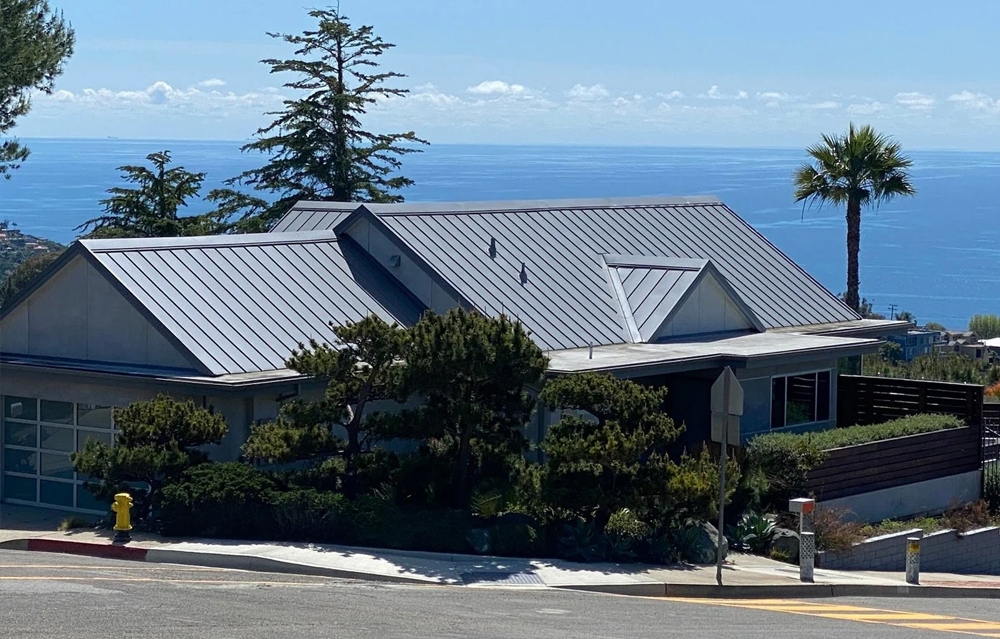
Making aluminum corrugated plate is a fairly simple process, but it does require some upfront planning. The main reason that this process is straightforward is that you need to control your variables. You can’t just go off and try to pull the corrugation out of aluminum by hand. To make the most efficient use of your time and resources, you need to plan ahead and do everything in a controlled setting. Aluminum Corrugation vs. Flute: What’s the Difference?
What is Aluminum Corrugated Plate?
An aluminum corrugated plate (ACP) is made from rectangular aluminum sheets that are corrugated to form a ribbed surface. Aluminum is a very common material for making corrugated products because of its cost, ease of process and high strength. Aluminum sheets can be corrugated in a wide range of widths and thicknesses to meet specific product requirements. Aluminum corrugated products are available in a variety of grades to suit a range of end-use applications. They are primarily used in packaging, transportation, construction and industrial markets.
Aluminum Corrugation Tips
– Use a corrugating machine. If you have access to a corrugating machine, you can try to corrugate aluminum sheets manually. But this will take a lot of time and effort. Plus, you will probably make a lot of mistakes. – Buy corrugated paper with a higher thickness than the product you want to make. For example, if you are making a box for food, buy the thinnest paper. The cardboard should be 3/8″ or 1/4″, but you corrugate the aluminum sheet to 1/8″ so that it fits better in the box. – Use aluminum sheet with a thickness of at least 0.062″ (1.57mm). Thicker aluminum sheets can be corrugated, but they produce less corrugation per sheet of paper. – Test the corrugation by holding a piece of corrugated paper up to a light source. If you can see the ribs through the paper, you’re corrugating the paper well. – For best results, corrugate paper that has been stored in a cool, dry place.
The Parts of a Corrugated Sheet
Top board – This is the top edge of the corrugated sheet. Ribs – These are the grooves in the aluminum sheet. Flutes – These are the spaces in between the ribs.
How to Make Aluminum Corrugated Plate
Step 1: Measure, mark and cut the aluminum sheets. Aluminum sheets come in a large range of widths, so it is best to measure and cut them to the desired size. You can also buy pre-cut aluminum sheets. If you have access to a sheet-metal shop or a mill, you can have the sheets cut there. Step 2: Super-crimp the edges of the aluminum sheets. This step is good for two reasons. First, you are making a very strong joint. Second, you are covering up any sharp edges where the sheets meet. Step 3: Assemble the corrugated sheet. After you have the corrugated sheet together and the joints are super-crimp, you are ready to start working with it. Step 4: Attach the sheet to the corrugating machine. In this step, you attach the corrugating machine to the aluminum sheet. You will likely be attaching it to an edge so that you can use it with a saw blade or other cutting tool. Step 5: Start the corrugating process. You will lower the corrugating pressure in stages as you move the upper and lower blades over the sheet. Step 6: Stop the corrugating process. As you move the upper and lower blades over the sheet, the corrugated plate will be pushed and pulled from the inside. When the material has been pushed between the blades to form a complete cylinder, you will release the sheets from the blade.
Wrapping Up
Aluminum corrugated plates are a fairly simple product to make. Once you have the parts, it’s just a matter of assembling them and then running them through a corrugating machine. This article provided a step-by-step guide to making aluminum corrugated plates. If you follow these instructions, you should be able to make your own ACP sheets.