Insulated aluminum composite panel (ACP) is a popular building material used in modern architecture. It is a sandwich panel consisting of two aluminum sheets bonded to a non-aluminum core material, such as polyethylene, fire-retardant mineral-filled core, or a honeycomb core. The panels are known for their durability, lightweight, and thermal insulation properties.
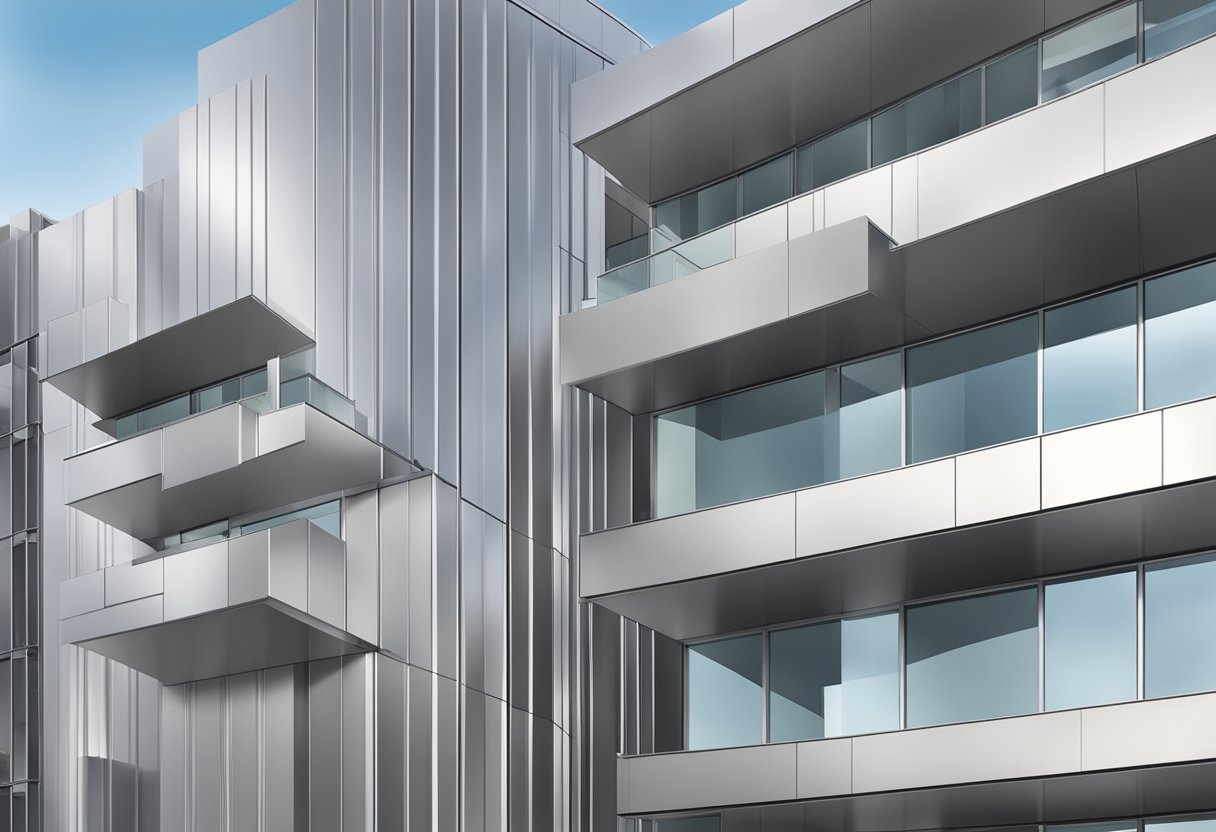
The use of insulated aluminum composite panels has become increasingly popular due to their versatility and aesthetic appeal. They are commonly used in commercial and residential buildings for exterior cladding, interior decoration, and signage. The panels are available in a wide range of colors, finishes, and sizes, allowing architects and designers to create unique and striking designs.
Insulated aluminum composite panels offer numerous benefits, including energy efficiency, fire resistance, and ease of installation. They are also environmentally friendly, as they can be recycled and reused. However, it is important to note that not all insulated aluminum composite panels are created equal, and proper installation and maintenance are crucial for ensuring their longevity and safety.
Composition of Insulated Aluminum Composite Panels
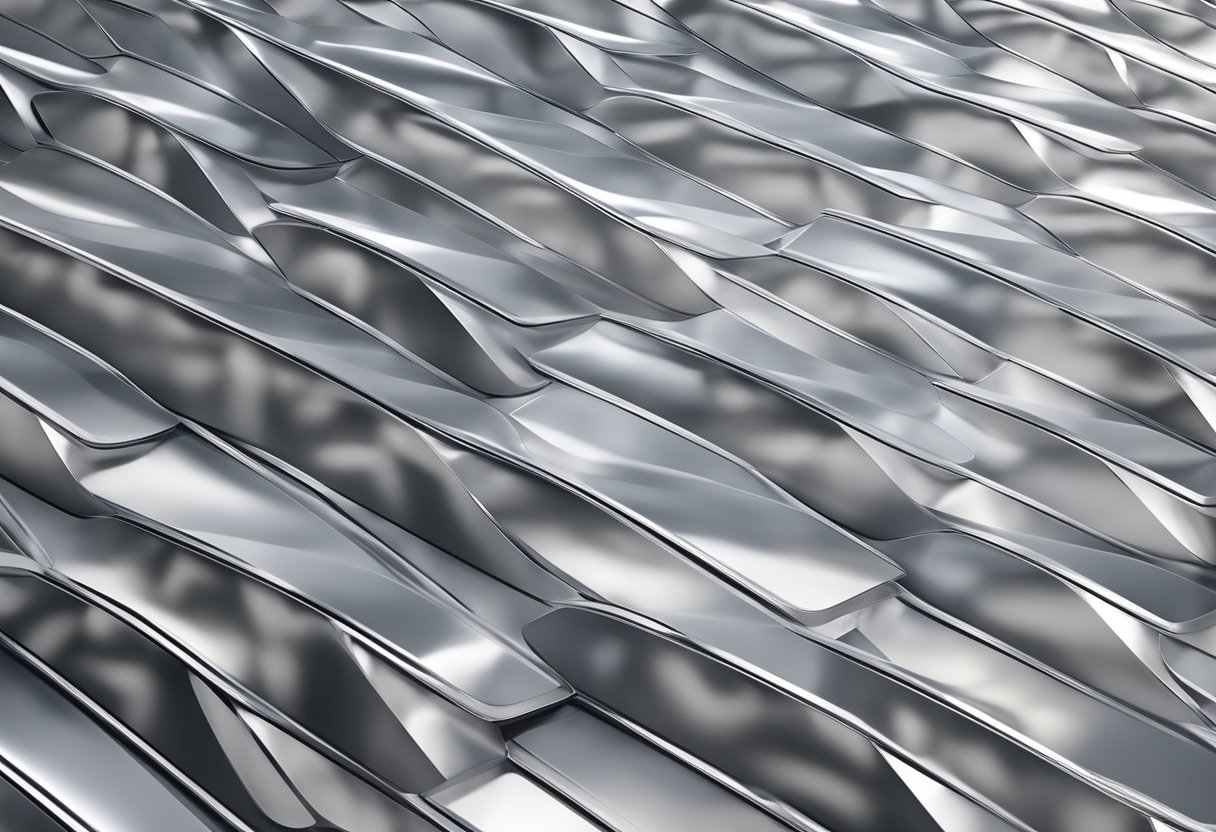
Insulated aluminum composite panels (ACP) are a popular building material that consists of two aluminum sheets bonded to a core material. The core material is typically made of a non-combustible mineral-filled core or a polyethylene foam core. The aluminum sheets are coated with a variety of finishes, including polyvinylidene fluoride (PVDF), polyester, or anodized aluminum.
Core Materials
The core material of an insulated aluminum composite panel is a crucial component that determines the panel’s fire resistance, insulation, and soundproofing properties. The two most common core materials used in ACPs are:
- Mineral-filled core: This core material is made of non-combustible minerals such as aluminum hydroxide and magnesium hydroxide. Mineral-filled cores are known for their excellent fire resistance and are often used in high-rise buildings and other structures that require strict fire safety standards.
- Polyethylene foam core: This core material is made of a lightweight foam material that provides excellent insulation and soundproofing properties. Polyethylene foam cores are less fire-resistant than mineral-filled cores and are often used in low-rise buildings and other structures that do not require strict fire safety standards.
Aluminum Layers
The two aluminum sheets that make up an insulated aluminum composite panel are typically made of 3000 or 5000 series aluminum alloys. These alloys are known for their excellent strength, durability, and corrosion resistance. The thickness of the aluminum sheets can vary depending on the application, with thicker sheets providing better impact resistance.
Coating Types
The aluminum sheets of an insulated aluminum composite panel are coated with a variety of finishes to provide protection against weathering, corrosion, and other environmental factors. The most common coating types used in ACPs are:
- Polyvinylidene fluoride (PVDF): This coating type is known for its excellent weather resistance and durability. PVDF coatings are commonly used in high-end architectural applications.
- Polyester: This coating type is less expensive than PVDF and is often used in low-rise buildings and other structures that do not require high-end finishes.
- Anodized aluminum: This coating type provides excellent corrosion resistance and is often used in industrial and commercial applications.
Overall, insulated aluminum composite panels are a versatile and durable building material that offers a wide range of benefits, including fire resistance, insulation, and soundproofing properties.
Manufacturing Process
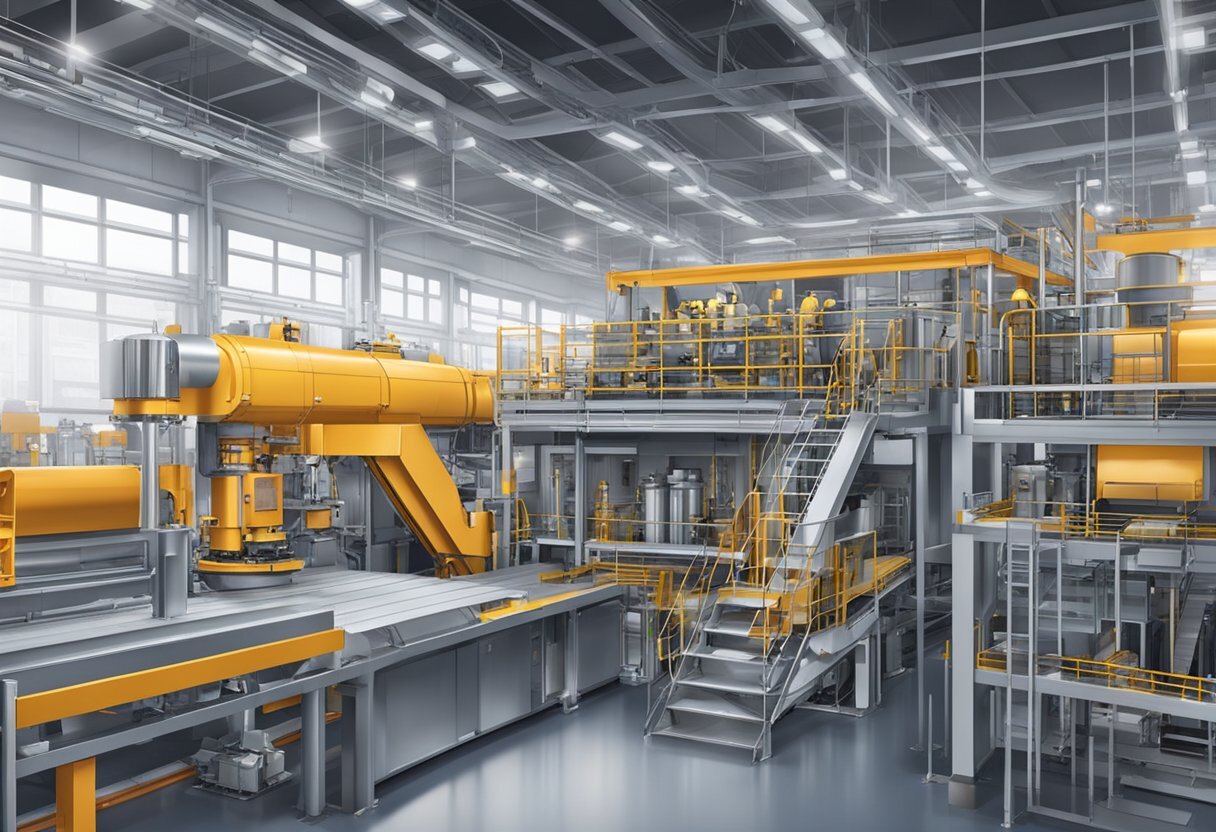
Material Preparation
The first step in manufacturing insulated aluminum composite panels is preparing the materials. The aluminum sheets are cleaned and coated with a primer to ensure better adhesion to the core material. The core material, typically made of polyethylene, is also prepared by cutting it into the required size and thickness.
Panel Lamination
Once the materials are prepared, the panel lamination process begins. The aluminum sheets and core material are fed into a laminating machine where they are bonded together using heat and pressure. The adhesive used in this process is typically a high-strength polymer that ensures a strong bond between the layers.
During the lamination process, the panels are also subjected to a series of quality control checks to ensure that they meet the required specifications. These checks include measuring the thickness of the panel, checking for any defects or imperfections, and verifying the adhesion strength between the layers.
Cutting and Finishing
After the lamination process is complete, the panels are cut to the required size and shape using a CNC machine. This ensures precision and accuracy in the cutting process. The panels are then finished by adding any required surface coatings, such as paint or anodizing, to improve their durability and appearance.
Overall, the manufacturing process for insulated aluminum composite panels involves several steps, each of which is critical in ensuring the quality and performance of the final product. Through careful preparation, lamination, and finishing, manufacturers are able to produce high-quality panels that meet the needs of a wide range of applications.
Thermal Performance
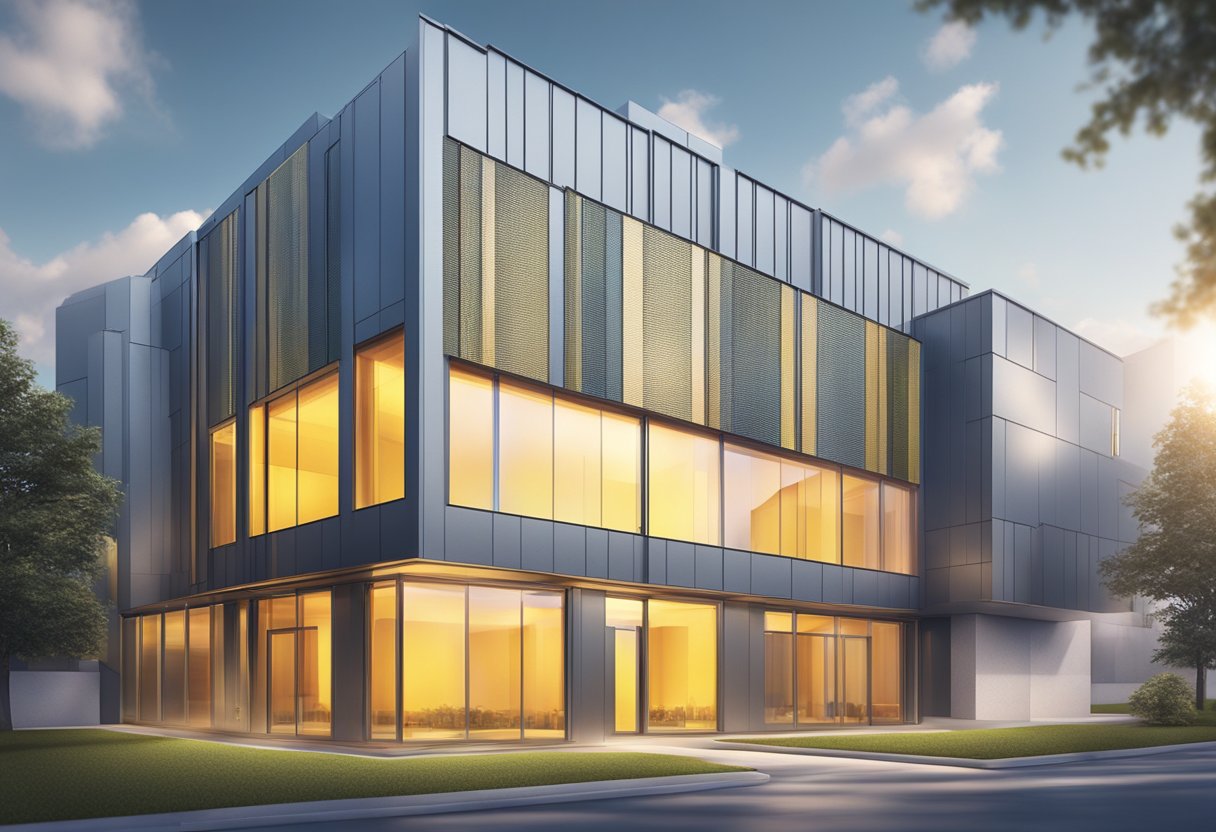
Insulation Properties
Insulated aluminum composite panels are known for their excellent insulation properties. The panels consist of a core material, typically made of polyethylene, which is sandwiched between two aluminum sheets. The core material provides insulation, while the aluminum sheets offer protection and durability.
The insulation properties of the panels depend on the thickness and type of core material used. Thicker cores provide better insulation, while different types of core materials offer varying levels of thermal resistance.
Energy Efficiency
Insulated aluminum composite panels are highly energy-efficient. The panels help to reduce the amount of energy needed to heat or cool a building, resulting in lower energy bills and a smaller carbon footprint.
The energy efficiency of the panels is due to their insulation properties. The panels help to keep the interior of a building at a consistent temperature, reducing the need for heating or cooling systems to work harder to maintain a comfortable environment.
In addition, the panels are lightweight and easy to install, reducing the amount of energy needed for transportation and installation. Overall, insulated aluminum composite panels are an excellent choice for those looking to improve the energy efficiency of their building.
Structural Features
Panel Strength
Insulated aluminum composite panel (ACP) is known for its high strength-to-weight ratio. This is due to its unique sandwich structure, which consists of two aluminum outer layers and a core made of polyethylene or fire-retardant mineral-filled core material. The panel’s strength comes from the combination of these layers, which work together to provide a rigid and durable surface.
Durability
Insulated ACP is highly durable and resistant to weathering, corrosion, and impact. The aluminum outer layers provide protection against harsh weather conditions, while the core material provides insulation and soundproofing. The panels are also resistant to fire, making them a popular choice for buildings that require high levels of fire safety.
Load Resistance
Insulated ACP is designed to withstand heavy loads and stresses. The panels have a high load-bearing capacity and can support large amounts of weight without buckling or bending. This makes them ideal for use in high-rise buildings, bridges, and other structures where strength and durability are critical.
In summary, insulated aluminum composite panel is a highly versatile and durable building material that offers excellent strength-to-weight ratio, weather resistance, fire safety, and load-bearing capacity. These features make it an ideal choice for a wide range of applications, from commercial and industrial buildings to residential homes and public spaces.
Design Flexibility
Insulated aluminum composite panels provide a wide range of design options for architects and builders. With its sleek and modern appearance, it is a popular choice for contemporary building designs.
Aesthetic Options
Insulated aluminum composite panels come in a variety of colors and finishes, allowing for endless design possibilities. The panels can be customized to match any desired color or pattern, making it easy to achieve a unique and eye-catching design.
In addition, the panels can be cut and shaped into different sizes and shapes, making it easy to create intricate designs and patterns. The panels can also be installed horizontally or vertically, adding to the design flexibility.
Customization Potential
Insulated aluminum composite panels can be customized to meet the specific needs of any project. The panels can be made thicker or thinner depending on the insulation requirements of the building.
Moreover, the panels can be combined with other materials such as glass, stone, or wood to create a unique and visually appealing design. The panels can also be perforated or embossed to create a textured or patterned surface.
Overall, insulated aluminum composite panels provide a high degree of design flexibility, making it a popular choice for modern building designs.
Installation Techniques
Tools and Equipment
Before starting the installation process of insulated aluminum composite panels, one must ensure that they have all the necessary tools and equipment. The following list includes some of the essential tools required for the installation process:
- Cordless drill
- Circular saw
- Jigsaw
- Measuring tape
- Level
- Screwdriver
- Hammer
- Safety equipment (gloves, safety glasses, hard hat)
Safety Measures
The installation of insulated aluminum composite panels requires some safety measures to be taken to avoid any accidents. The following list includes some of the safety measures that must be taken:
- Always use safety equipment, including gloves, safety glasses, and a hard hat.
- Ensure that the installation area is free from any obstacles.
- Make sure that the panels are not damaged during transportation and handling.
- Use appropriate lifting equipment to avoid any injuries.
- Follow the manufacturer’s instructions and guidelines.
Best Practices
Proper installation techniques are crucial to ensure the longevity and performance of the insulated aluminum composite panels. The following list includes some of the best practices for the installation process:
- Ensure that the panels are installed on a flat and even surface.
- Use appropriate fasteners to secure the panels to the structure.
- Leave a gap of at least 10mm between the panels to allow for thermal expansion.
- Use the appropriate sealant to seal the joints and edges of the panels.
- Follow the manufacturer’s guidelines for cleaning and maintenance.
Overall, the installation of insulated aluminum composite panels requires the use of appropriate tools and equipment, adherence to safety measures, and following the best practices to ensure a successful installation.
Applications
Architectural Uses
Insulated aluminum composite panels are widely used in the construction industry for various architectural purposes. These panels are used in building facades, cladding, roofing, and partitions. The panels are lightweight and easy to install, which makes them an ideal choice for high-rise buildings and large-scale construction projects. The panels come in a variety of colors and finishes, which allows architects to create unique and aesthetically pleasing designs.
The panels are also highly durable and weather-resistant, which makes them suitable for use in harsh environments. They are resistant to corrosion, fading, and chalking, which helps to maintain the appearance of the building over time. The panels also have excellent thermal insulation properties, which helps to reduce energy consumption and lower heating and cooling costs.
Industrial Purposes
Insulated aluminum composite panels are also used in various industrial applications. They are used in the manufacturing of transportation vehicles, such as buses, trains, and airplanes. The panels are lightweight, which helps to reduce the weight of the vehicle and improve fuel efficiency. The panels are also highly durable and resistant to impact, which helps to protect the vehicle from damage.
The panels are also used in the manufacturing of industrial equipment and machinery. They are used to create protective enclosures, partitions, and barriers. The panels are highly resistant to chemicals and moisture, which helps to protect the equipment from corrosion and damage. The panels also have excellent fire resistance properties, which helps to prevent the spread of fire in industrial settings.
In conclusion, insulated aluminum composite panels have a wide range of applications in the construction and industrial sectors. Their lightweight, durability, and weather-resistant properties make them an ideal choice for various architectural and industrial purposes.
Regulatory Standards
Building Codes
Insulated aluminum composite panels are subjected to various building codes that regulate their use in construction projects. The International Building Code (IBC) and the National Fire Protection Association (NFPA) are two of the most important codes that regulate the use of these panels. These codes specify the minimum requirements for the use of composite panels in construction projects.
Fire Safety
Fire safety is a critical aspect of construction projects, and insulated aluminum composite panels must comply with fire safety regulations. The panels must meet the fire safety requirements of the IBC and the NFPA. These regulations require that the panels be tested and certified to meet specific fire safety standards. The panels must also be installed in accordance with the manufacturer’s instructions to ensure their fire safety.
Environmental Regulations
Insulated aluminum composite panels must also comply with environmental regulations. The panels must not contain any hazardous materials that can harm the environment or human health. The Environmental Protection Agency (EPA) regulates the use of these panels and their disposal. The panels must be disposed of in accordance with the EPA’s regulations to avoid any negative impact on the environment.
In summary, insulated aluminum composite panels must comply with various regulatory standards, including building codes, fire safety regulations, and environmental regulations. These panels must be tested and certified to meet specific standards and must be installed and disposed of in accordance with the regulations to ensure their safety and environmental friendliness.
Performance Testing
Quality Assurance
Before insulated aluminum composite panels are released for use, they undergo a series of quality assurance tests to ensure that they meet industry standards. These tests include a visual inspection for any defects or imperfections, as well as a test of the panel’s strength and durability. In addition, the panels are tested for their resistance to fire, water, and other environmental factors that may affect their performance.
Durability Tests
Insulated aluminum composite panels are designed to withstand extreme weather conditions and other environmental factors. To ensure their durability, these panels are subjected to a variety of tests, including impact resistance, wind load resistance, and corrosion resistance. These tests are designed to simulate real-world conditions and ensure that the panels can withstand the rigors of daily use.
Thermal Analysis
Insulated aluminum composite panels are designed to provide excellent thermal insulation, helping to reduce energy costs and improve overall energy efficiency. To ensure that these panels meet industry standards for thermal performance, they are subjected to a variety of tests, including thermal conductivity and thermal resistance tests. These tests are designed to measure the panel’s ability to transfer heat and provide insulation, helping to ensure that the panels meet the highest standards for energy efficiency.
Maintenance and Care
Cleaning Procedures
Insulated aluminum composite panels require regular cleaning to maintain their appearance and performance. The cleaning frequency depends on the location and environmental conditions of the panels. The following cleaning procedures are recommended:
- Use a soft-bristled brush or a cloth to remove loose dirt and debris from the panel surface.
- Prepare a cleaning solution by mixing mild soap or detergent with water in a bucket. Avoid using abrasive cleaners or solvents as they can damage the panel surface.
- Dip a sponge or a soft cloth in the cleaning solution and apply it to the panel surface.
- Rinse the panel surface thoroughly with clean water to remove the cleaning solution.
- Dry the panel surface with a clean, soft cloth or allow it to air dry.
Inspection Guidelines
Regular inspections of insulated aluminum composite panels can help identify any damage or defects that require repair. The following inspection guidelines are recommended:
- Inspect the panel surface for any signs of damage, such as cracks, dents, or scratches.
- Check the panel joints and edges for any signs of separation or delamination.
- Inspect the panel surface for any signs of discoloration or fading.
- Check the panel mounting system for any signs of corrosion or damage.
Repair Techniques
Insulated aluminum composite panels can be repaired using various techniques depending on the type and extent of damage. The following repair techniques are recommended:
- Small scratches or dents can be repaired using touch-up paint or filler.
- Larger scratches or dents may require panel replacement or professional repair.
- Separated or delaminated panels can be repaired using adhesive or mechanical fasteners.
- Corroded mounting systems should be replaced with new ones.
Regular maintenance and care of insulated aluminum composite panel can help extend their lifespan and maintain their performance. It is important to follow the recommended cleaning procedures and inspection guidelines to identify any damage or defects that require repair.
Environmental Impact
Recyclability
Insulated aluminum composite panels are highly recyclable. The panels are made of two thin aluminum sheets with a non-aluminum core material. The aluminum sheets can be easily separated from the core material, allowing for efficient recycling. The recycled aluminum can be used to manufacture new panels or other aluminum products, reducing the need for virgin materials.
Lifecycle Assessment
A lifecycle assessment of insulated aluminum composite panel shows that they have a low environmental impact. The panels have a long lifespan and require little maintenance, reducing the need for replacement. The energy required to manufacture the panels is relatively low, and the panels are lightweight, reducing transportation emissions.
The non-aluminum core material used in the panels can vary, and some materials may have a higher environmental impact than others. However, many manufacturers are using eco-friendly core materials, such as recycled plastic or bio-based materials, to reduce the environmental impact of the panels.
Overall, insulated aluminum composite panel are a sustainable and environmentally friendly choice for building facades.